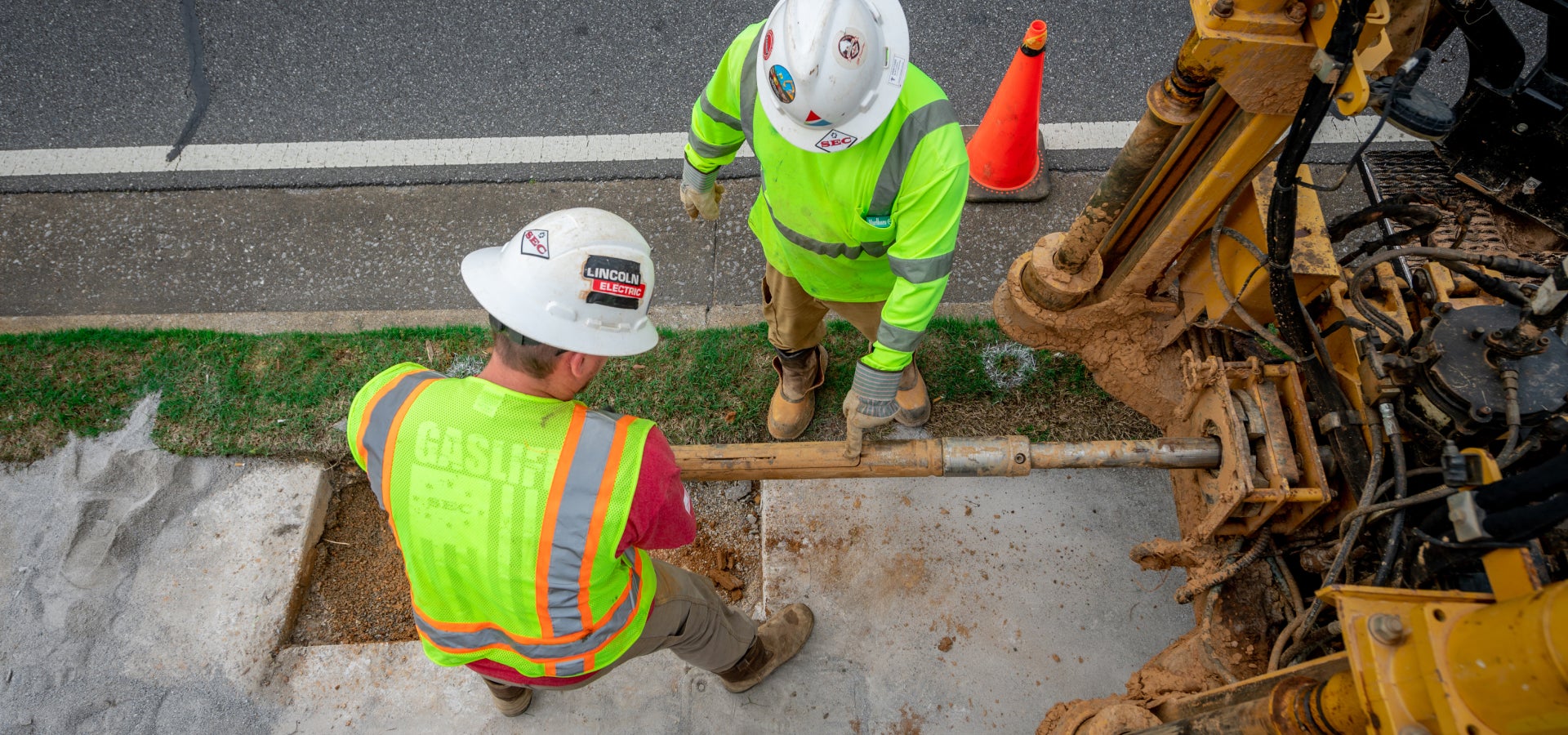
Vintage Plastic Replacement Program
The use of plastic pipe in natural gas distribution systems became prevalent in the 1960s and has increased steadily over time. The early generation plastics or “vintage” plastics used in distribution systems have since caused maintenance issues and increased risk profiles for many natural gas operators. Operators are now targeting existing vintage plastic pipelines for replacement.
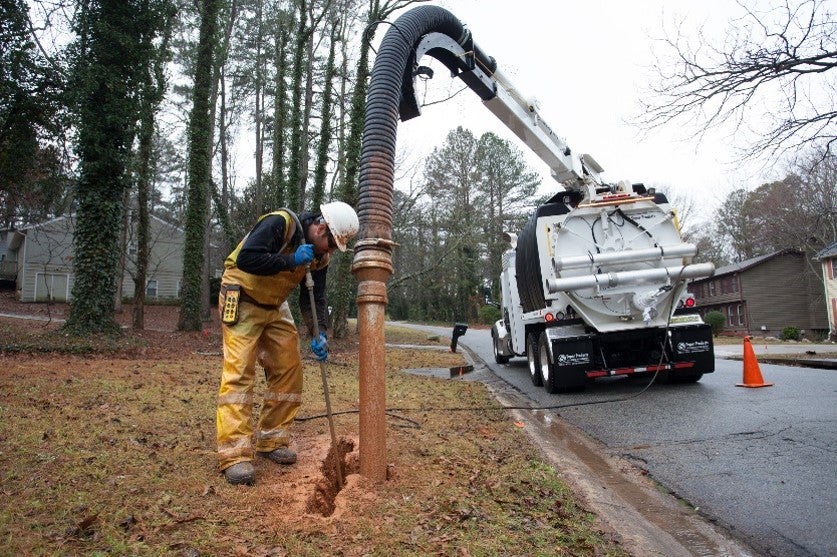

One of the challenges associated with replacing vintage plastic pipelines is the sheer volume of underground utilities surrounding these lines. At the same time vintage plastics were being installed to the right of way with water and sewer, other utilities such as power lines and phone cables were beginning to be placed underground. In later years, cable TV and fiber internet were installed. It is not uncommon to have 4-6 utilities in the same right-of-way with vintage plastic natural gas pipelines. This underground congestion makes it difficult to install new pipelines using traditional construction methods, such as trenching or horizontal directional drilling, without damaging utilities already in the ground.
In search of providing a better solution to limit damages to surrounding utilities and provide a better experience for customers, SEC refined and eventually perfected its pipe splitting process and procedures. SEC’s pipe splitting procedure allows new pipe to be inserted inside the old vintage plastic pipe.
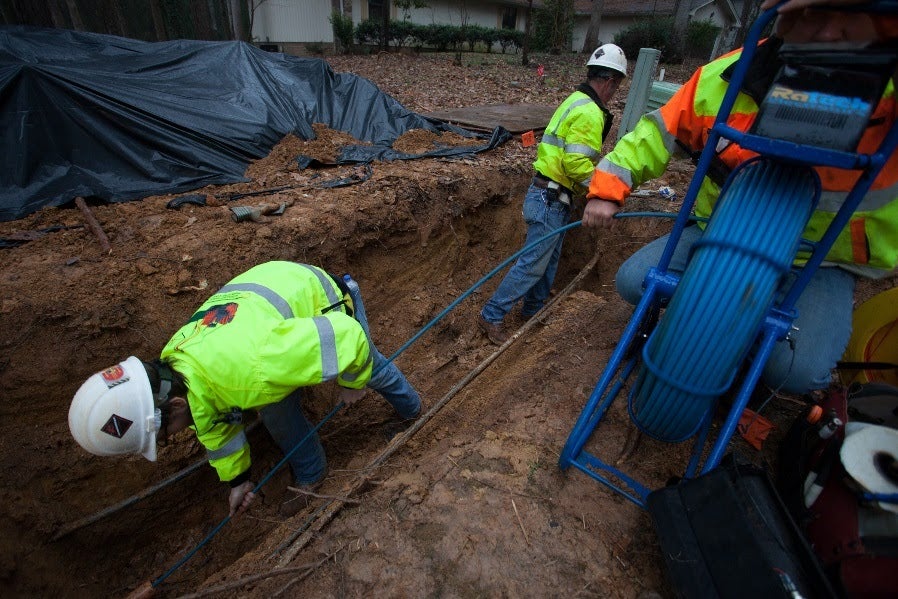
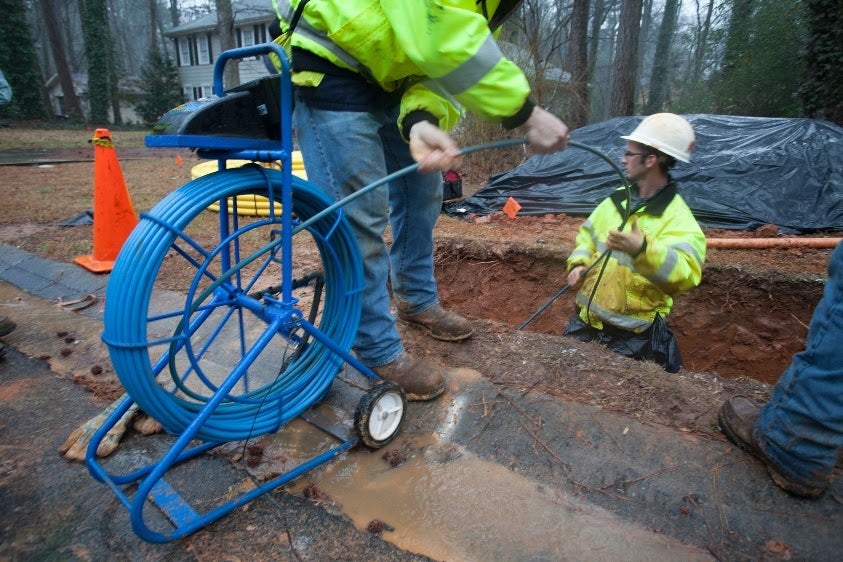
Pipe splitting has many advantages. By installing the new pipe in the same exact path as the existing vintage plastic pipeline, we save valuable right-of-way space and greatly reduce the potential for utility damages that might be caused by trenching, excavating, or drilling for the installation of a new line. Pipe splitting requires that we put gas on newly installed mains and services the same day we retire the existing main and services, shortening the construction process for a segment of main from weeks/months to one or two days. This eliminates leaks on the system sooner, eliminates the risk associated with parallel active mains, and improves the customer and property owner experience greatly. Learn more about the process below.
Pipe Bursting/Splitting has many advantages. Crews are able to work quickly and efficiently and the old pipe is retired that day. The process reduces the possibility of damaging utilities and speeds up the overall project. Lastly, the process reduces clean up time and disruption to property.

ISOLATION PROCESS
Gauges are set upstream and downstream of the section of gas main to be taken out of service to ensure gas pressure is maintained on either side of the isolation. SEC can provide a CNG Trailer downstream of isolation if required (typical for one-way feeds).
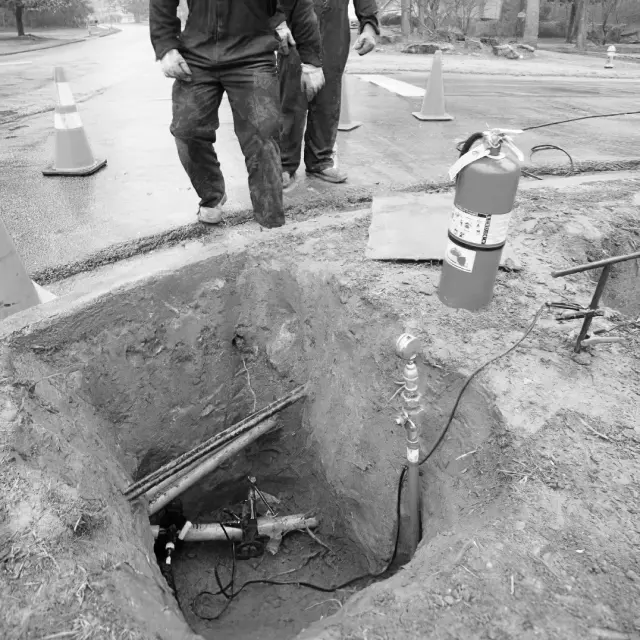
CAMERA EXISTING PIPE FOR POTENTIAL OBSTRUCTIONS
Once existing pipe is isolated, it is cut on both ends and internally inspected with a camera for potential obstructions to the splitting process. Items like metal fittings or elbows will be cut out.
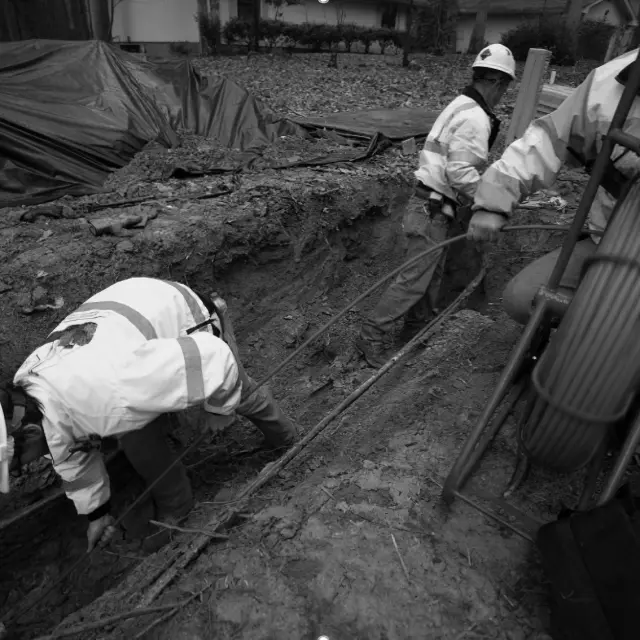
PIPE SPLITTING
A cable attached to a wench is pulled through the pipe. Once through the pipe, a splitting ahead and expander is attached to the cable and pulled back through the existing pipe by wench with new plastic pipe in tow. Once pulled through, the pipe is ready to be tested, tied-in, and purged with gas.
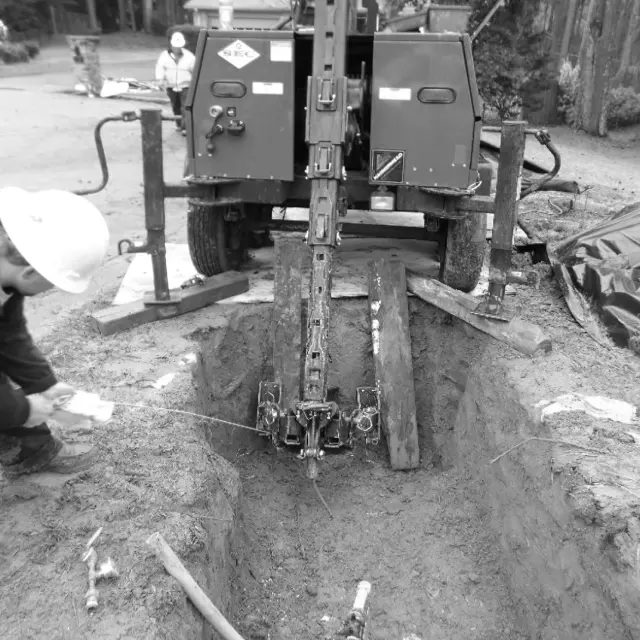
LOCATE EXISTING UTILITIES
Locate all existing utilities in ROW. Ensure existing gas lines to be split are of adequate depth. Visually spot all utilities at perpendicular crossings to ensure adequate clearance exists. Hydro-excavation is the preferred method for spotting utilities around Vintage Plastics. (Show picture of guy spotting with HydroVac).
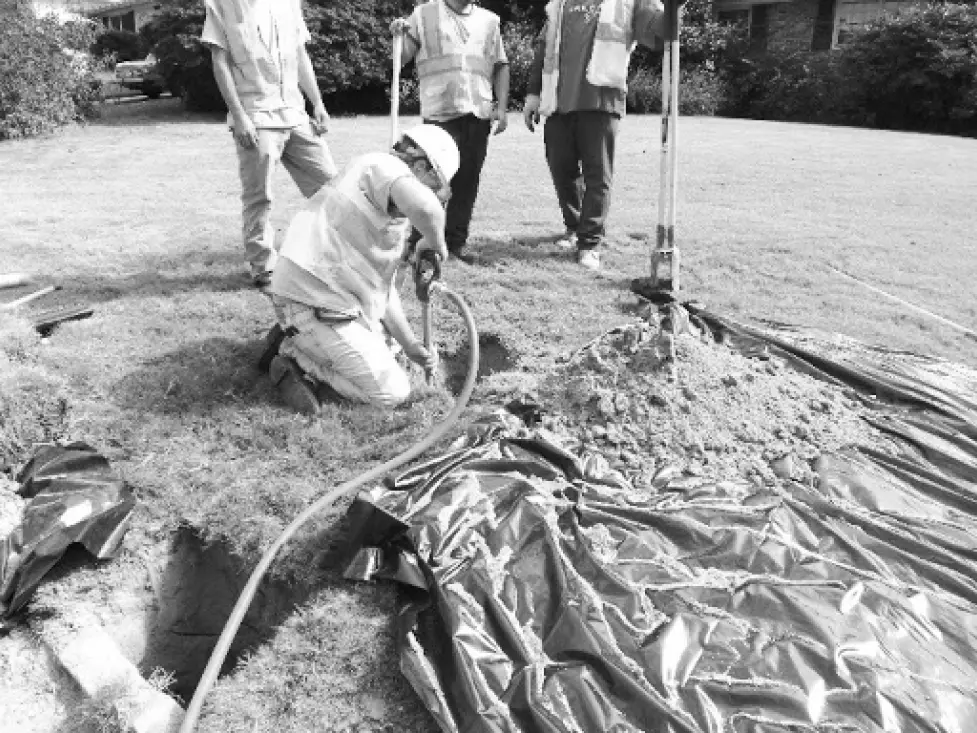
Pipe splitting reduces damages in congested environments.